Galvanizing
Innovative suspension galvanizing line for making Zn zinc coatings on steel details.
We have galvanic bathtubs allowing galvanizing of components with dimensions L x W x H [mm]:
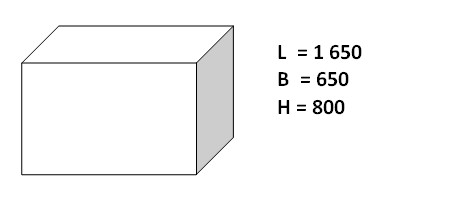
and galvanic drums for galvanizing of small details.
The electroplating process involves surface treatment of details at subsequent process stations of the line in galvanizing tanks, in which details are subject to:
- degreasing,
- pickling,
- decapping,
- galvanizing,
- passivation,
- drying.
Between the process baths there are rinsing tanks, the so-called washers.
Innovation in the proposed galvanizing technology is based on continuous homogenization and mixing of galvanic baths by the following methods:
- mechanical,
- magnetic,
- electric,
which will ensure access of the electrolyte containing Zn to the entire surface of the coated detail (including complex ones such as threads and holes, …) and maintaining a constant concentration of Zn in the bath.
The above has been achieved by:
1. Introduction of the coated detail and / or the bathtub to mechanical vibrations at ultrasonic frequency.
The use of ultrasound is one of the latest technological solutions in the field of metallurgy. Vibrations ensure better penetration of Zn into the areas of a detail with a complicated shape (holes, depressions, …) and unify the composition of the bath solution in the area of the surface of the coated detail.
2. Introduction of magnetic agitators into the bath (Fe wires coated with Teflon).
The use of this method is a particularly beneficial solution for covering parts with very deep holes, where the use of ultrasound may not be sufficient.
3. Introduction to the galvanizing process of an additional process of cleaning out metallic particles using magnets.
This avoids galvanic bath poisoning – reduces or eliminates the harmful environmental effect.
4. The use of automatic control and maintaining a constant Zn concentration by measuring the current, the magnitude of which is stabilized by the level of galvanization voltage and the active surface of zinc anodes in the electrolyte.
5. Application of additional coating of components with a protective varnish-resin coating containing Zn.
To increase the corrosion resistance of the zinc coating, an additional layer of varnish is applied to it by hot immersion or by cold spraying.